Team:UC Davis/Safety
From 2012.igem.org
(Difference between revisions)
Line 771: | Line 771: | ||
<br>2. Callura, Jared, Dwyer, Daniel, Isaacs, Farren, Cantor, Charles, Collins, James. “Tracking, tuning, and terminating microbial physiology using synthetic riboregulators”. PNAS vol. 107 no. 36, pp. 15898-15903. Web. 13 July 2010. | <br>2. Callura, Jared, Dwyer, Daniel, Isaacs, Farren, Cantor, Charles, Collins, James. “Tracking, tuning, and terminating microbial physiology using synthetic riboregulators”. PNAS vol. 107 no. 36, pp. 15898-15903. Web. 13 July 2010. | ||
<br>3. “Gene Overview”, <i>Imperial College London iGEM Wiki 2011</i>. | <br>3. “Gene Overview”, <i>Imperial College London iGEM Wiki 2011</i>. | ||
+ | <br><br> | ||
+ | <b>1. Would any of your project ideas raise safety issues in terms of: researcher safety, public safety, or environmental safety?</b> | ||
+ | |||
+ | <br><br> | ||
+ | |||
+ | The accumulation of plastic products poses a hazard to the environment, as well as humans, through drinking water contamination. This threat led us to develop a degradation pathway to turn the polyethylene terephthalate into different substrates. We produce terephthalic acid and ethylene glycol. Ethylene glycol is a moderately toxic substance, which is oxidized to glycolic acid. The glycolic acid is further oxidized to oxalic acid – a toxic substance that affects the central nervous system via the liver. However, in the environment, the ethylene glycol will be degraded by hydroxyl radicals and in sewage sludge, it is readily biodegradable. Because ethylene glycol must be ingested to pose a problem, researchers take extra precaution to make sure there are no splashes of ethylene glycol in the laboratory and the wastes will be disposed of in the appropriate hazardous waste receptacles. Ethylene glycol can also be a mild irritant if it comes in contact with the skin or if it is inhaled, so researchers wear eye protection as well as gloves and lab coats, and always work with ethylene glycol in the confine of a fume hood. Also, in our constructs, we have produced enzymes that will degrade ethylene glycol into glycoaldehyde and then glycolate. The glycolate has the potential to be turned in to oxaloacetate, a metabolic intermediate. In the environment, ethylene glycol can potentially be toxic within waterways, however the team made sure to dispose of ethylene glycol in a responsible way. | ||
+ | |||
+ | <br><br><br> | ||
+ | |||
+ | <b>2. Do any of the new BioBrick parts (or devices) that you made this year raise any safety issues? If yes, did you document these issues in the Registry? How did you manage to handle the safety issue? How could other teams learn from your experience?</b> | ||
+ | |||
+ | <br><br> | ||
+ | |||
+ | Our BioBrick parts this year do not raise safety issues, despite the ethylene glycol production. The safety management procedures have been discussed in the previous question’s answer. The novel part that we are submitting to the Registry is the cutinase gene, in BioBrick format. This is a lipolytic enzyme that does not pose a threat to humans. | ||
+ | |||
+ | <br><br><br> | ||
+ | |||
+ | <b>3. Is there a local biosafety group, committee, or review board at your institution? If yes, what does your local biosafety group think about your project? If no, which specific biosafety rules or guidelines do you have to consider in your country?</b> | ||
+ | |||
+ | <br><br> | ||
+ | |||
+ | The University of California at Davis has a biosafety group, which heads the disposal and use of hazardous materials. They approve of our project and the procedures that we have followed. Further, they are excited for the potential that this project has, in terms of making the environment safer for inhabitants. | ||
+ | |||
+ | <br><br><br> | ||
+ | |||
+ | <b>4. Do you have any other ideas how to deal with safety issues that could be useful for future iGEM competitions? How could parts, devices and systems be made even safer through biosafety engineering?</b> | ||
+ | |||
+ | <br><br> | ||
+ | |||
+ | Safety issues could be headed by a designated safety monitor in each iGEM group. This set-up allows all of the teams to have a person who will always make sure that the safest procedures are being followed at all times. Also, the production of potentially hazardous materials should always be controlled by an inducible promoter, so that it may be stopped at any time. The different parts can be made safer by making the parts work only with BioBrick assembly units and nothing else that exists in nature. | ||
+ | |||
</article> | </article> | ||
</div> | </div> |
Revision as of 20:16, 29 August 2012
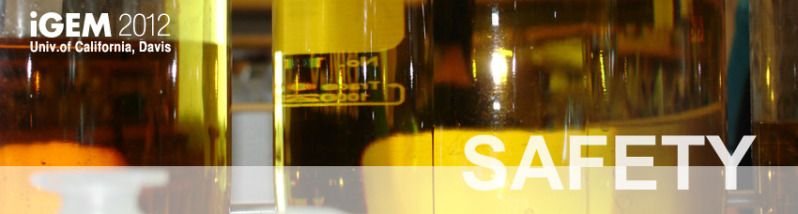
News
- Presented our respective project at the UC San Francisco campus. We interacted with teams from UC Berkeley, UCSF, and Stanford-Brown.
- Requested the protocal from the iGEM Washington 2011 team, July 10th.
- Field trip to Yolo County Landfill, June 27th. Met with Ramin Yazdani, the senior civil engineer at the landfill.
- Sushi buffet for lunch, June 21st
- First day of iGEM meeting, June 18th
Criteria
View our judging criteria for iGEM 2012 here.Safety
Our team made sure to perform a thorough analysis of safety for all parts of our project, since safety for researchers, the public, and the environment are all important. We work within a Level 2 Biosafety Lab, as defined by the Laboratory Biosafety Manual (1). This facility is well equipped to work with all the strains of E. coli we used. We used MG1655, DH5α, and K12, all of which are Risk Level 1, meaning these strains pose no pathogenic risk to humans, and were completely contained within the lab.
We always made sure to make use of protective gear, such as wearing gloves at all times, masks when using UV lamps, and lab coats when appropriate. All of our waste was autoclaved on site as well, and all tools and glassware thoroughly cleaned after each use.
We worked with ethylene glycol during our experiments, which is toxic to the kidney, liver and central nervous system, as well as a skin and eye irritant. Obviously, we wanted to be very safe when using this chemical, so we made sure to consult with our advisers on how best to handle it. When using ethylene glycol, we always worked under a fume hood and wore lab coats. We had a separate waste bottle for all of the byproducts with ethylene glycol, so that the waste could be treated.
The University of California at Davis has a biosafety group, which heads the disposal and use of hazardous materials. They approve of our project and the procedures that we have followed. Further, they are excited for the potential that this project has, in terms of making the environment safer for inhabitants.
Our BioBricked parts do not raise any safety concerns, as long as the enzymes breaking down ethylene glycol are fully functional.
Our project, when properly functioning, should not have any harmful effect on the environment, researchers, or the public. We keep everything contained within the lab, and all of the plates and wastes are autoclaved to prevent all bacteria we use from spreading to the outside environment. If we were to escalate our project to an industrial level, everything would still be contained within the facility.
If we were to implement our bacteria in a landfill, chances are it could not survive past a couple generations and therefore would not be very toxic. However, if we were to imagine a more robust version of our strain created in the future, we would implement a kill switch, which has already been created using synthetic biology, to make sure we could stop it (2). We would also create a system similar to Imperial College London’s Gene Guard, which would stop to plastic-degrading plasmid from getting transferred to other bacteria (3). This would contain the plasmid within only our bacteria, so it would not get out of hand.
Our project could potentially be dangerous if our strain received a pathogenic plasmid by lateral gene transfer from other organisms. However, if this were a concern, our strain would be just a susceptible to pathogenicity as any other. If someone with malicious intent were to use our construct, perhaps the most they could do is release it into the water way and have it degrade plastic pipes made of PET, or modify it to degrade other plastics in addition to PET and degrade something useful. Cutinase, the first enzyme in our degradation pathway, functions optimally at 50° C, and the water in our pipes would most likely not be at that temperature. Also, it is unlikely the strain would survive under conditions such as this temperature and being in an aquatic environment.
1. Laboratory Biosafety Manual. The World Health Organization. 2004. 3rd edition.
2. Callura, Jared, Dwyer, Daniel, Isaacs, Farren, Cantor, Charles, Collins, James. “Tracking, tuning, and terminating microbial physiology using synthetic riboregulators”. PNAS vol. 107 no. 36, pp. 15898-15903. Web. 13 July 2010.
3. “Gene Overview”, Imperial College London iGEM Wiki 2011.
1. Would any of your project ideas raise safety issues in terms of: researcher safety, public safety, or environmental safety?
The accumulation of plastic products poses a hazard to the environment, as well as humans, through drinking water contamination. This threat led us to develop a degradation pathway to turn the polyethylene terephthalate into different substrates. We produce terephthalic acid and ethylene glycol. Ethylene glycol is a moderately toxic substance, which is oxidized to glycolic acid. The glycolic acid is further oxidized to oxalic acid – a toxic substance that affects the central nervous system via the liver. However, in the environment, the ethylene glycol will be degraded by hydroxyl radicals and in sewage sludge, it is readily biodegradable. Because ethylene glycol must be ingested to pose a problem, researchers take extra precaution to make sure there are no splashes of ethylene glycol in the laboratory and the wastes will be disposed of in the appropriate hazardous waste receptacles. Ethylene glycol can also be a mild irritant if it comes in contact with the skin or if it is inhaled, so researchers wear eye protection as well as gloves and lab coats, and always work with ethylene glycol in the confine of a fume hood. Also, in our constructs, we have produced enzymes that will degrade ethylene glycol into glycoaldehyde and then glycolate. The glycolate has the potential to be turned in to oxaloacetate, a metabolic intermediate. In the environment, ethylene glycol can potentially be toxic within waterways, however the team made sure to dispose of ethylene glycol in a responsible way.
2. Do any of the new BioBrick parts (or devices) that you made this year raise any safety issues? If yes, did you document these issues in the Registry? How did you manage to handle the safety issue? How could other teams learn from your experience?
Our BioBrick parts this year do not raise safety issues, despite the ethylene glycol production. The safety management procedures have been discussed in the previous question’s answer. The novel part that we are submitting to the Registry is the cutinase gene, in BioBrick format. This is a lipolytic enzyme that does not pose a threat to humans.
3. Is there a local biosafety group, committee, or review board at your institution? If yes, what does your local biosafety group think about your project? If no, which specific biosafety rules or guidelines do you have to consider in your country?
The University of California at Davis has a biosafety group, which heads the disposal and use of hazardous materials. They approve of our project and the procedures that we have followed. Further, they are excited for the potential that this project has, in terms of making the environment safer for inhabitants.
4. Do you have any other ideas how to deal with safety issues that could be useful for future iGEM competitions? How could parts, devices and systems be made even safer through biosafety engineering?
Safety issues could be headed by a designated safety monitor in each iGEM group. This set-up allows all of the teams to have a person who will always make sure that the safest procedures are being followed at all times. Also, the production of potentially hazardous materials should always be controlled by an inducible promoter, so that it may be stopped at any time. The different parts can be made safer by making the parts work only with BioBrick assembly units and nothing else that exists in nature.